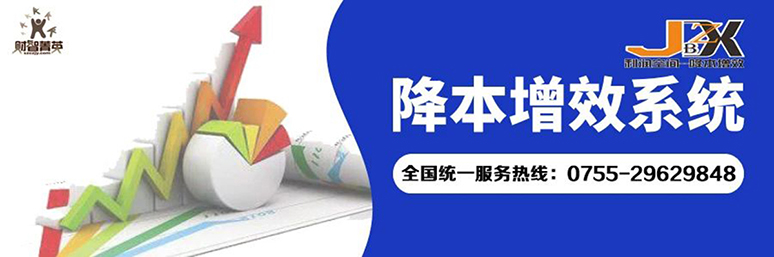
2021年5月7日—9日,广东中泰龙集团130多(duō)位中高层管理(lǐ)人员共同研习《利润空间—降本增效系统》;中泰龙集团董事長(cháng)、总裁、各分(fēn)子公司总经理(lǐ)出席参加了实训营。
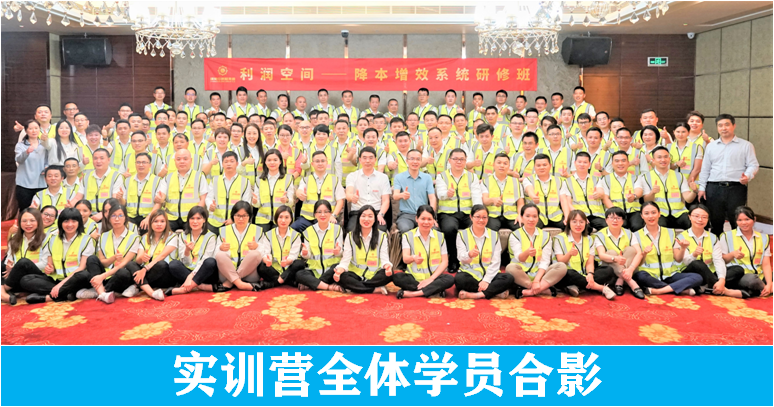
3天3夜实训营,每天學(xué)习与训练时间超过12个小(xiǎo)时,无论是白天理(lǐ)论知识學(xué)习环节,还是晚上实操做降本增效蓝本方案环节,各个小(xiǎo)组争先恐后,PK如火如荼;學(xué)在苦中求,艺在勤中练。实训营的口号是:要得会,就得累;要得精,用(yòng)命拼。
3天3夜实训营,姜上泉导师团队3位咨询导师共同剖析了降本增效的五项内容:
通过做好研销协同、产供协同、业财协同,规划增效与降本的目标;目标制定需要关注三张财務(wù)报表、三张运营报表、四个财務(wù)数据(年度利润目标数据、损益平衡点数据、竞争对手报价数据、管理(lǐ)失败成本数据);目标制定需要符合SMART的原则,目标分(fēn)解需要符合对上支撑性和对下承接性的原则。透过“产品力、品牌力、渠道力”3力的打造,把产品卖贵和卖好,消除不给产品或服務(wù)增加价值的活动,并对营销资源进行合理(lǐ)而有(yǒu)效的配置,把重要而关键的资源集中在优质客户上。
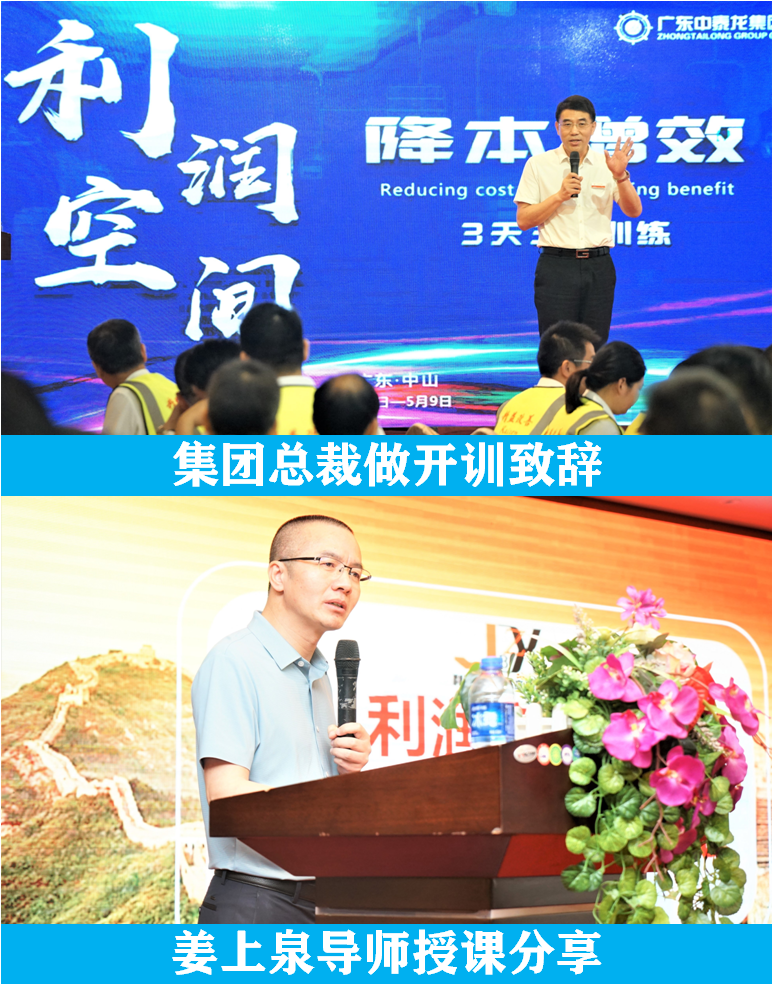
运用(yòng)研发与销售协同的工具,实现产品的好卖;运用(yòng)USP、SPIN、FAB等方法,实现产品的卖好;通过对客户、产品、通路的盈利能(néng)力分(fēn)析和改善,实现产品毛利率的增長(cháng)。
通过3力模型、四会能(néng)力、五朵梅花(huā)、六大策略做好营销的增量增效。零件的标准化,部件的通用(yòng)化,带来产品的系列化,产品的系列化带来成本的低减化。通过模组化设计缩短开发周期时间以降低研发成本,运用(yòng)通用(yòng)化设计减少零部件的数量以降低材料成本,运用(yòng)平台化设计和少件化设计减少加工工时以降低人工成本。
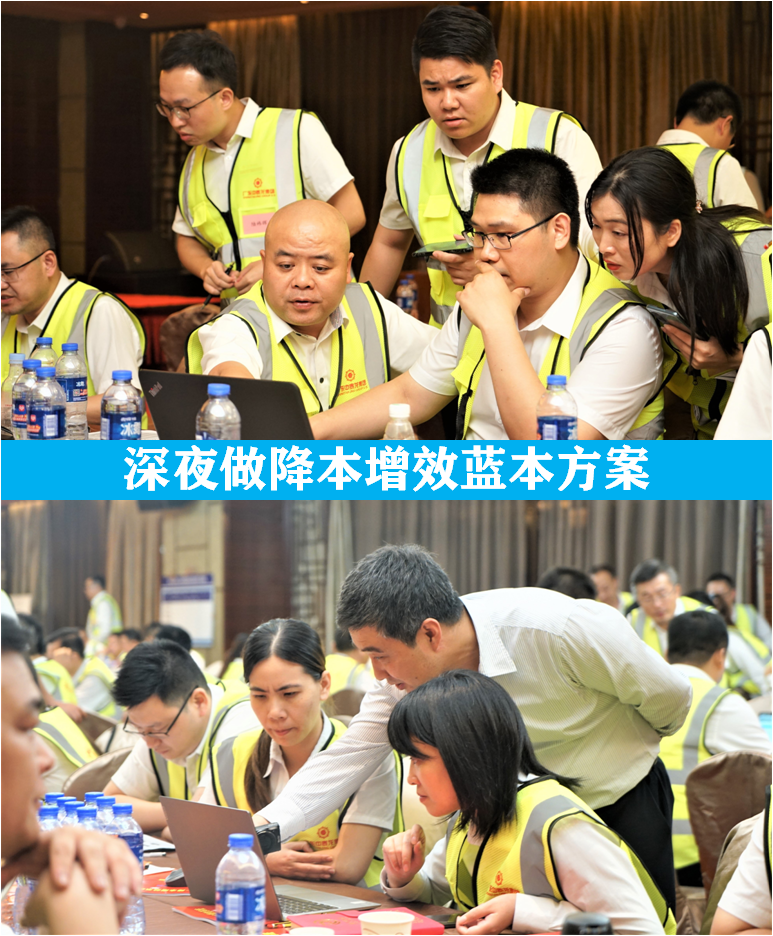
企业80%的产品成本锁定在设计阶段,70%的库存是由设计人员决定的,产品不良80%是设计不良造成的。透过研发降本增效10步法、TRIZ创新(xīn)设计、设计优化、功能(néng)优化、工艺优化,在设计阶段就将产品成本控制到最低。
抓住“采購(gòu)降本增效8大指标”与“采購(gòu)降本增效4.0模型”的“牛鼻子”,实现采購(gòu)总成本的控制与削减。
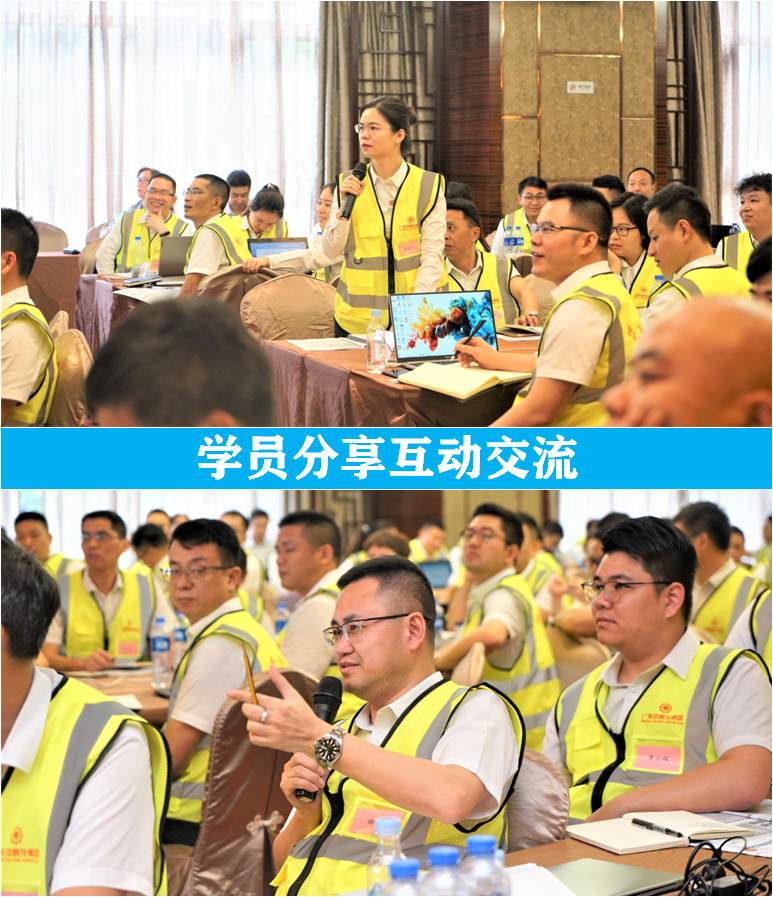
采購(gòu)总成本改善,改进采購(gòu)过程及价格谈判的贡献率是11%,供应商(shāng)改进质量的贡献率是14%,利用(yòng)供应商(shāng)开展JIT即时生产的贡献率是20%,利用(yòng)供应商(shāng)的技术与工艺的贡献率是40%,供应商(shāng)参与产品开发的贡献率是42%。无论是运用(yòng)ESI和EPI降低采購(gòu)成本,还是采用(yòng)分(fēn)阶段蚕食谈判砍价降低采購(gòu)成本,采購(gòu)总成本的改善,是个永恒的主题。管理(lǐ)者不改善不创新(xīn)就是工作失职,一流的企业没人知道有(yǒu)浪费,人人改善浪费;二流的企业有(yǒu)人知道有(yǒu)浪费,有(yǒu)人改善浪费;三流的企业人人知道有(yǒu)浪费,没人改善浪费。浪费改善先宏观后微观,先整體(tǐ)后局部;浪费改善大处看布局和流程,小(xiǎo)处看工序和动作。姜上泉导师剖析了运用(yòng)五看法、五比法发现流程浪费和损失,运用(yòng)五改法消除流程浪费和损失。
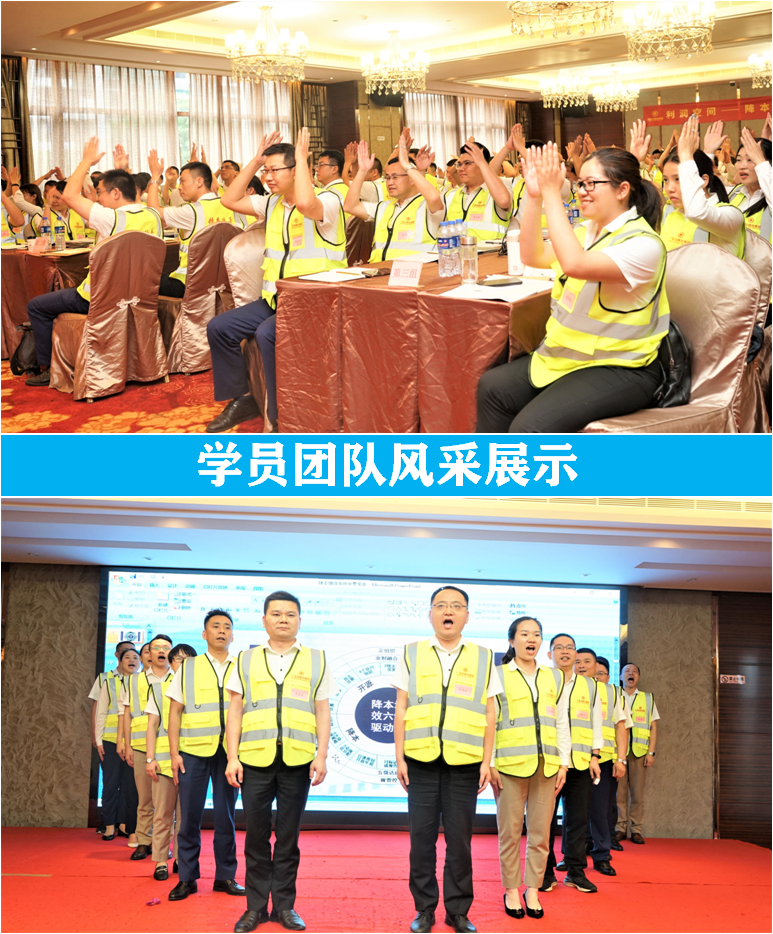
《利润空间—降本增效系统》实训营通过研销协同、产供协同、业财协同实现增效与降本;业務(wù)線(xiàn)通过战略降本增效、研发降本增效、工艺降本增效、采購(gòu)降本增效、物(wù)流降本增效、生产降本增效、质量降本增效、人资降本增效、营销创收增效促进企业利润提升;财務(wù)線(xiàn)通过年度经营计划、全面预算、管理(lǐ)会计、独立经营體(tǐ)机制改善企业经营业绩。